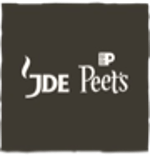
Everyday billions of cups of coffee and tea are enjoyed across the globe. Our belief is that together, through the power of our brands, we can unite our actions to deliver impactful change and be a ‘force for better’. The JDE Peet’s Common Grounds programme embodies our ambition to positively impact people, our planet, and the future of coffee and tea.
SOURCING FOR BETTER
We are championing regenerative agriculture to enhance livelihoods and positively impact our planet.
TOWARDS PLANET POSITIVE
We are striving towards a planet-positive supply chain through innovation and collaboration on sustainable solutions.
PUTTING PEOPLE FIRST
We are engaging colleagues and communities through the joy of coffee and tea to support wellbeing and promote equal opportunity.
For more on our sustainability journey read our integrated annual report.
For more on our external recognition.